A production manager typically supervises workers in a factory or manufacturing plant to ensure efficiency. He or she determines the quantity of certain items to be produced, inspects the quality of workmanship on finished goods, and schedules regular maintenance on machinery. In addition, the production manager is often involved in making shipping arrangements with distribution centers and retail stores. Managers usually need to possess strong communication and problem-solving skills to make sure that manufacturing processes run smoothly and that workers are kept safe at all times.
Production managers usually work on-site in factories to monitor activity and give directions to workers. Executives and other supervisors provide managers with information about market demand and budgets so that they can set production schedules. They make sure that daily quotas are met by keeping workers on task and informed of procedural changes. If production falls behind for any reason, managers can determine the best ways to get back on schedule.
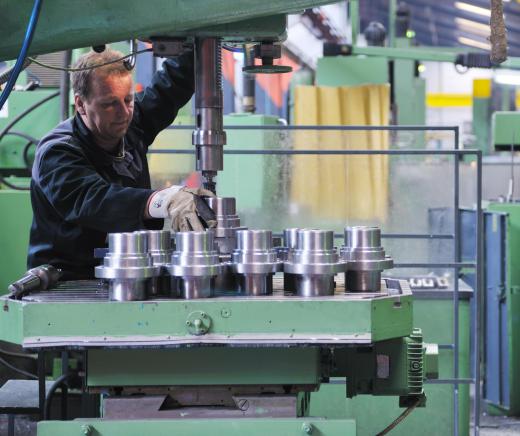
Many managers are also responsible for hiring and training new workers. They conduct regular performance reviews and meet individually with workers to help them identify ways to improve their techniques. Whenever workers have suggestions or concern, the production manager is usually the first point of contact.
Implementing quality control policies typically is an essential part of a production manager's job. The manager designs detailed product quality checklists and monitors items as they are constructed. Every item is scrutinized before it can be packaged and shipped in many small factories. In large manufacturing plants, a sample of products that come off of the assembly line is selected at random to undergo careful inspection and testing to ensure that they contain no defects. The production manager might perform personal inspections or oversee a group of quality-control workers.
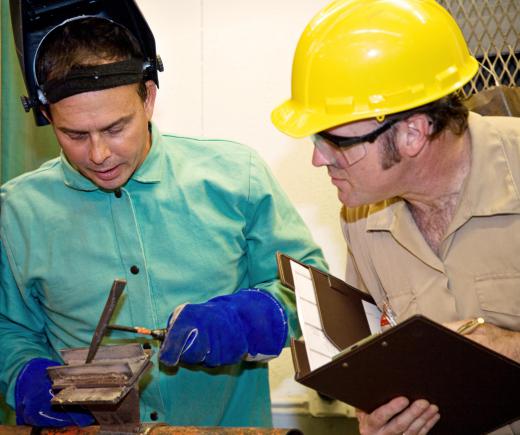
Routine preventive maintenance on manufacturing equipment can be important to avert potential standstills in production. The manager is responsible for scheduling maintenance work and regular inspections on equipment to make sure that machines are clean, safe, and running efficiently. He or she determines the need for new machinery and orders replacement parts when necessary.
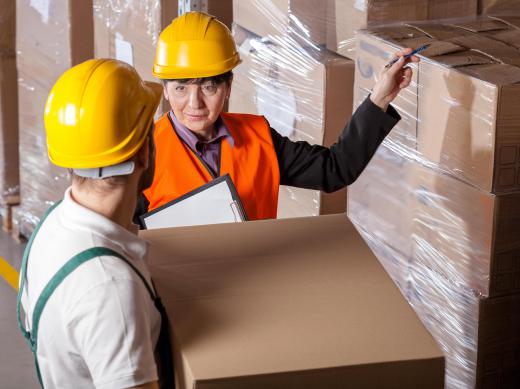
Most production managers hold bachelor's degrees or higher in business administration or industrial management. They usually begin their careers as floor workers or assistant managers in a factory, and advance to supervisory positions after gaining experience and exhibiting strong leadership skills. With continuing education in business administration, many professionals who excel in production management positions eventually assume head manager or executive roles in their companies.